Hardware Overview
Board Dimensions
The board dimensions are illustrated in the drawing below; the listed measurements are in inches.
Board dimensions (PDF) for the TMC6300 motor driver breakout board, in inches.
Need more measurements?
For more information about the board's dimensions, users can download the eagle files for the board. These files can be opened in Eagle and additional measurements can be made with the dimensions tool.
Eagle - Free Download!
Eagle is a CAD program for electronics that is free to use for hobbyists and students. However, it does require an account registration to utilize the software.
Dimensions Tool
This video from Autodesk demonstrates how to utilize the dimensions tool in Eagle, to include additional measurements:
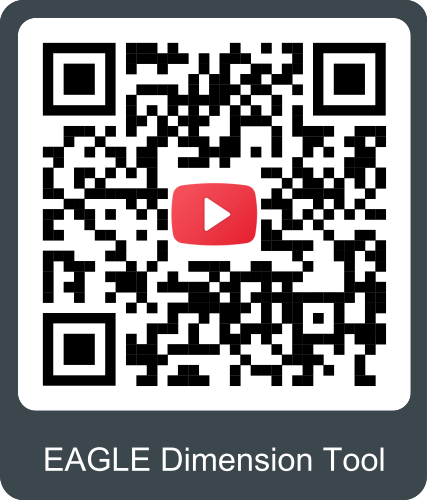
Power
Users are provided with PTH to connect their external power supply, I/O logic-level voltage, and the regulated 1.8V output. The TMC6300 motor driver has an input voltage range of 2.0V to 11.0V.
The power connections on the TMC6300 motor driver.
Below, is a general summary of the circuitry on the board:
VIN
- Power supply input- Range: 2 to 11V
VIO
- I/O supply voltage- Range: 1.8 to 5.25V
NSTDBY
- IC goes to standby mode and resets when this pin is pulled toGND
VCP
- Charge pump voltageGND
- The common ground or the 0V reference for the board
Info
For more details, users can reference the schematic and the TMC6300 datasheets.
Motor Voltage
Even though the input voltage range for the motor driver goes down to 2V, users will need to provide the minimum operating voltage for their motor. Our Gimbal Stabilizer Motor has an operating voltage range of 6 - 8V.
Power LED
The red, power (PWR
) LED will light up when a power supply is connected to the board. However, the LED can be disabled for low-power applications by cutting the jumper.
The PWR
status LED indicator for the TMC6300 motor driver.
VIO
/Standby Pin
In it's default configuration, the VIO
pin is used to enable the motor driver and set the logic level voltage (1.8 to 5.25V) for the I/O pins. However, the VIO
pin also operates as a standby pin when it is pulled LOW
. In standby, the TMC6300 resets and sits in standby mode.
VIO
pin on the TMC6300 motor driver.
VCP
Pin
The VCP
pin is broken out for users to include an external charge pump capacitor. Adding an external capacitor would help stabilize the supply voltage, from the large voltage swings (dV/dt) of the motor driver's operation. A 1nF to 100nF capacitor rated at 10V, is recommended by the datasheet.
VCP
pin on the TMC6300 motor driver.
TMC6300
The TMC6300 from Trinamic Motion Control, part of Analog Devices, is a low voltage, 3-Phase BLDC/PMSM motor driver utilizing separate high-side and low-side control signals for its three half-bridges.
Info
For more details, please refer to the TMC6300 datasheet and application note.
Chip Protections
The TMC6300 features the overtemperature and short protections:
- The overtemperature protection feature implements a two temperature thresholds; however, the datasheet warns users that this should only be relied on as an emergency percaution and may not prevent the destruction of the IC. This is due to several factors including that excess heat can generate quickly before the overtemperature sensor can react. Therefore, users should prevent this situation from occuring by design with methods such as adequate heat dissipation.
- The short protection feature gaurds the motor commutation channels by monitoring the current flowing through each of the power stage MOSFETs. Once a short condition (short to
GND
orVS
) is safely detected, all driver bridges become switched off, and theDIAG
output becomes set. In order to restart the motor, the users must must disable and restart the TMC6300. As with the overtemperature protection, the datasheet warns users that this feature should only be relied on as an emergency percaution and may not prevent the destruction of the IC or detect all possible short events.
By monitoring the current draw through the SEN
pin, users can also implement an over current protection scheme in their software. This can also aid in preventing a trigger in the overtemperature protection and validating a short detection.
Maximum Load Current
When pushing the maximum load current of 2A, users should monitor the current draw through the SEN
pin and add a heat sink to provide additional heat dissipation. This should precautions can help to avoid damaging the IC.
Motor Commutation
The TMC6300 relies on an electrical commutation sequence/signal to drive the motor phases to a BLDC or PMSM motor. The commutation signals for these motors are trapezoidal for BLDC motors and sinusoidal for PMSM motors.
For a trapezoidal signal, the high-side (HS) and low-side (LS) MOSFETs, can just be driven high or low. However, in order to approximate a sinusoidal signal, a progressively varying PWM signal must be provided from the microcontroller and all six signal should be in sync with each other.
Sinusoidal PWM signal.
(Source: Demystifying BLDC motor commutation: Trap, Sine, & FOC)
PMSM vs BLDC Motor
A BLDC motor (sometimes referred to as a BLDM) and a PMSM (sometimes referred to as an AC synchronus motor) for the most part will appear the same in their internal construction. The difference between these types of motors is in their stator windings. This means that their commutation (the electrical signals used to drive the motor) is different.
- In a BLDC motor, the windings are concentrated on salient poles, requiring a voltage waveform that's more trapeziodal than sinusoidal.
- In a PMSM, the windings are distributed over several poles, requiring a voltage waveform that's more more sinusoidal.
Gimbal Motor
Based on measuring the output from one of the coils, our gimbal motor is a PMSM and would require a sinusoidal waveform to drive the motor. It should be noted that a trapezodial waveform can probably be used; however, users may notice effects such as cogging.
Alternative Use Cases
While this IC is intended to be used to drive 3-Phase BLDC/PMSM motors, users can easily adapt their hardware and software to work with other moters. For example, users could use two half-bridges to form an H-bridge and adapt their control software to drive a brushed, DC motor.
I/O Pins
There are several I/O pins for the TMC6300. Some of the pins are detailed in the power section above; the VOUT
pin is ommitted because it isn't broken out.
Half-Bridges
The TMC6300 features high-side and low-side MOSFET pairs of the three available half-bridges which control the commutation of the three motor phases.
6 PWM control of a 3-phase motor commutation.
(Source: Modified from the Block commutation vs. FOC in power tool motor control application note)
The electronic commutation sequence of these pins will depend on the motor that is connected. For most cases, users will provide a PWM signal to each of the pins. These are active-high pins with logic levels controlled by the VIO
pin.
UL
/UH
, VL
/VH
, and WL
/WH
) for the three half-bridges of the TMC6300 motor driver.
Active High
By pulling the pin high, the MOSFET will enable power to flow through that section of the half-bridge.
Microcontroller Limitations
Users will need to use pins capable of providing a PWM signal. In addition, for the recommended Simple FOC Arduino library, users will also need to consider the supported microcontroller as well as the configuration for the 6PWM mode.
With the electronic commutation sequence provided to the half-bridges, the output motor phases will drive a connected motor.
U
/V
/W
) from the TMC6300, used to drive a motor.
Wiring Sequence
For a 3-phase brushless motor, the connection sequence of the wires to a BLDC motor doesn't necessarily matter; the direction that the motor spins can be controlled through the software. However, for reference, switching two of the output channels to the motor will automatically reverse the direction that the motor was spinning.
- If users swap the
U
andV
connections, but leave theW
connection alone, the motor will now spin in the opposite direction of the original configuration.
Diagnostic Pin
The diagnostic pin is triggered based on different faults (i.e. shorts and overtemperature) detected by the IC. By default, the status will be indicated by the, green diagnostic, D
LED and will remail LOW
until triggered. Once triggered, users will need to disable and reset the TMC6300 or power cycle the board.
The DIAG
pin on the TMC6300 motor driver.
Users can also monitor the DIAG
pin, so their microcontroller knows when to reset the TMC6300 to clear the fault.
Current Sense Pin
The current sense pin is the foot point of the U
and V
half-bridges, with a 0.12Ω resistor attached. Users can measure the voltage across the SENSE
and GND
pins to determine the current flowing to the motor; however, it is recommended that an op-amp be attached to amplify the signal.
The SEN
pin on the TMC6300 motor driver.
LEDs
There are three status indicator LEDs on the TMC6300 motor driver:
V
- Power (Red)- Turns on once power is supplies to the
VIN
pin
- Turns on once power is supplies to the
D
- Diagnostics (Green)- Turns on to indicate a fault (see diagnostic pin section)
S
- Standby (Blue)- Turns on when the motor driver is enabled
- Turns off, when the IC has been reset and the motor driver is in standby mode
The status indicator LEDs on the TMC6300 motor driver.
Heat Sink Pad
A 0.13" x 0.14" platted copper pad is provided on the top of the board, where users can add a heat sink to dissipate excess heat generated by the TMC6300. The pad can accommodate the small heatsink in our catalog.
Thermal Shutdown Temperature
The AP329A has a 160°C (320°F) thermal shutdown temperature. The TMC6300 will restart automatically when the junction temperature decreases to +130°C.
Copper Heat Sink
Users may be tempted to use our copper heatsink on their board. However, we highly advise against using the copper heatsink because it barely fits and will likely cause a short across one of the pins.
Heat sink pad on the top of the TMC6300 motor driver.
Jumpers
Never modified a jumper before?
Check out our Jumper Pads and PCB Traces tutorial for a quick introduction!
There are three jumpers on the back of the board that can be used to easily modify a hardware connections on the board.
- V - This jumper can be used to remove power from the red, power LED.
- S - This jumper can be used to remove power from the blue, standby LED.
- D - This jumper can be used to remove power from the green, diagnostic LED.
The LED jumpers on the back of the TMC6300 motor driver.